Doel van coatingmaterialen
Het coaten van de buitenkant van stalen buizen is cruciaal om roestvorming te voorkomen. Roestvorming op het oppervlak van stalen buizen kan de functionaliteit, kwaliteit en uitstraling ervan aanzienlijk beïnvloeden. Het coatingproces heeft dan ook een aanzienlijke impact op de algehele kwaliteit van stalen buisproducten.
-
Vereisten voor coatingmaterialen
Volgens de normen van het American Petroleum Institute moeten stalen buizen minimaal drie maanden corrosiebestendig zijn. De vraag naar langere roestwerende periodes is echter toegenomen, waarbij veel gebruikers een roestwerende periode van drie tot zes maanden bij buitenopslag nodig hebben. Naast de duurzaamheidseis verwachten gebruikers dat coatings een glad oppervlak behouden en de corrosiewerende middelen gelijkmatig verdelen zonder lekken of druppels die de visuele kwaliteit zouden kunnen beïnvloeden.
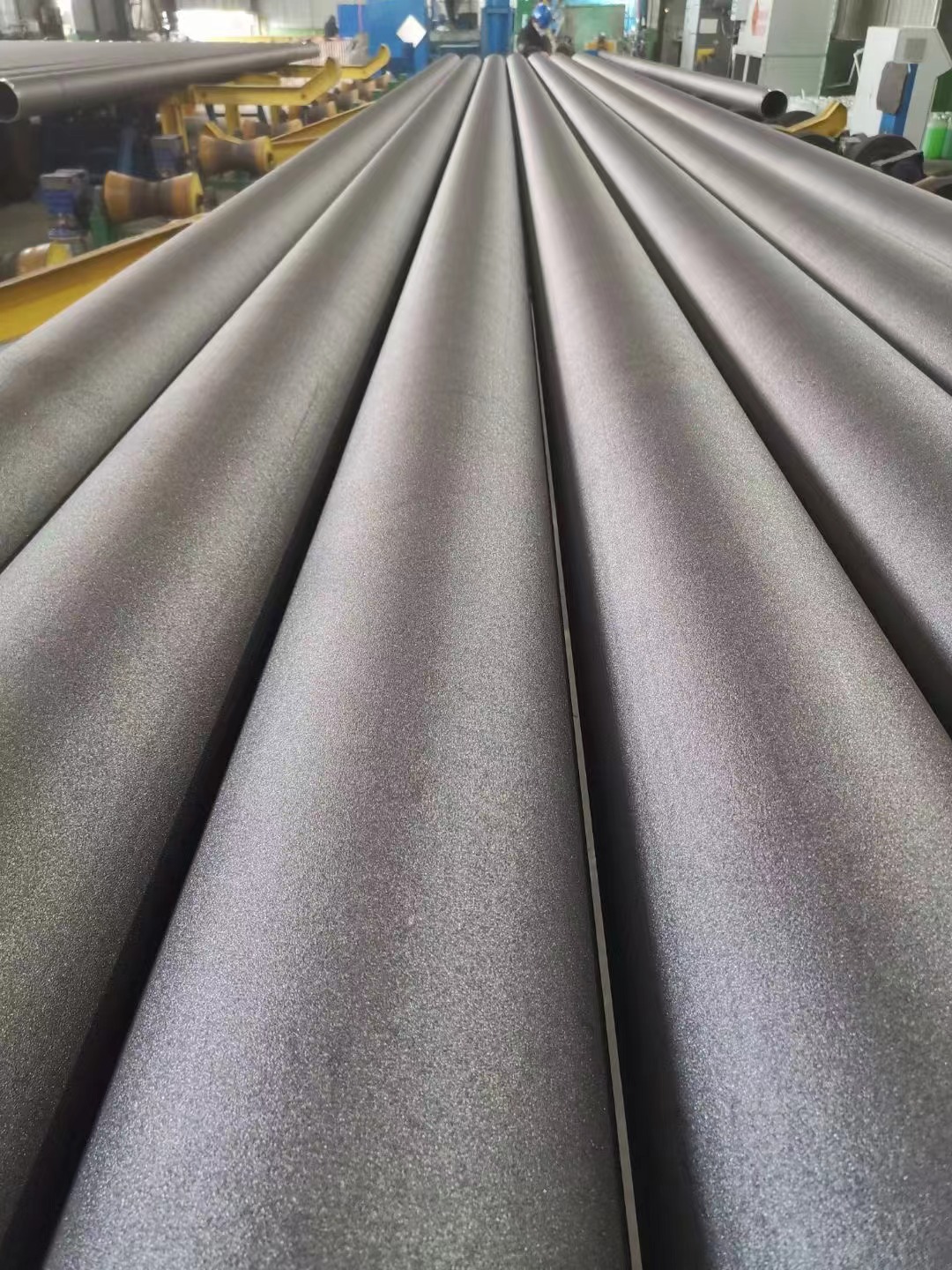
-
Soorten coatingmaterialen en hun voor- en nadelen
In stedelijke ondergrondse leidingnetwerken,stalen buizenworden steeds vaker gebruikt voor het transport van gas, olie, water en meer. De coatings voor deze leidingen zijn geëvolueerd van traditionele asfaltmaterialen naar polyethyleenhars en epoxyharsmaterialen. Het gebruik van polyethyleenharscoatings begon in de jaren 80 en met verschillende toepassingen zijn de componenten en coatingprocessen geleidelijk verbeterd.
3.1 Petroleumasfaltcoating
Petroleumasfaltcoating, een traditionele anticorrosieve laag, bestaat uit lagen petroleumasfalt, versterkt met glasvezeldoek en een externe beschermende polyvinylchloridefilm. Het biedt uitstekende waterdichtheid, goede hechting op diverse ondergronden en is kosteneffectief. Het heeft echter nadelen, waaronder gevoeligheid voor temperatuurschommelingen, broosheid bij lage temperaturen en veroudering en scheurvorming, vooral in rotsachtige bodems. Dit vereist extra beschermingsmaatregelen en hogere kosten.
3.2 Koolteer epoxy coating
Koolteerepoxy, gemaakt van epoxyhars en koolteerasfalt, vertoont uitstekende water- en chemicaliënbestendigheid, corrosiebestendigheid, goede hechting, mechanische sterkte en isolerende eigenschappen. Het vereist echter een langere uithardingstijd na het aanbrengen, waardoor het gevoelig is voor ongunstige weersomstandigheden gedurende deze periode. Bovendien vereisen de verschillende bestanddelen die in dit coatingsysteem worden gebruikt gespecialiseerde opslag, wat de kosten verhoogt.
3.3 Epoxypoedercoating
Epoxypoedercoating, geïntroduceerd in de jaren 60, houdt in dat poeder elektrostatisch op voorbehandelde en voorverwarmde buisoppervlakken wordt gespoten, waardoor een dichte corrosiewerende laag ontstaat. De voordelen hiervan zijn onder andere een breed temperatuurbereik (-60 °C tot 100 °C), sterke hechting, goede weerstand tegen kathodische onthechting, impact, flexibiliteit en lasschade. De dunnere film maakt het echter gevoelig voor beschadiging en vereist geavanceerde productietechnieken en -apparatuur, wat uitdagingen oplevert bij toepassing in het veld. Hoewel het op veel vlakken uitblinkt, schiet het tekort in vergelijking met polyethyleen wat betreft hittebestendigheid en algehele corrosiebescherming.
3.4 Polyethyleen anti-corrosieve coating
Polyethyleen biedt een uitstekende slagvastheid en hoge hardheid, en is bestand tegen een breed temperatuurbereik. Het wordt veel gebruikt voor pijpleidingen in koude gebieden zoals Rusland en West-Europa vanwege de superieure flexibiliteit en slagvastheid, vooral bij lage temperaturen. Er blijven echter uitdagingen bestaan bij de toepassing ervan op buizen met een grote diameter, waar spanningsscheuren kunnen optreden en binnendringend water corrosie onder de coating kan veroorzaken. Dit vereist verder onderzoek en verbeteringen in materiaal en applicatietechnieken.
3.5 Zware anti-corrosie coating
Zware anticorrosiecoatings bieden een aanzienlijk verbeterde corrosiebestendigheid in vergelijking met standaardcoatings. Ze zijn langdurig effectief, zelfs onder zware omstandigheden, met een levensduur van meer dan 10 tot 15 jaar in chemische, maritieme en oplosmiddelhoudende omgevingen, en meer dan 5 jaar in zure, basische of zoute omstandigheden. Deze coatings hebben doorgaans een drogelaagdikte van 200 μm tot 2000 μm, wat zorgt voor superieure bescherming en duurzaamheid. Ze worden veel gebruikt in maritieme constructies, chemische apparatuur, opslagtanks en pijpleidingen.
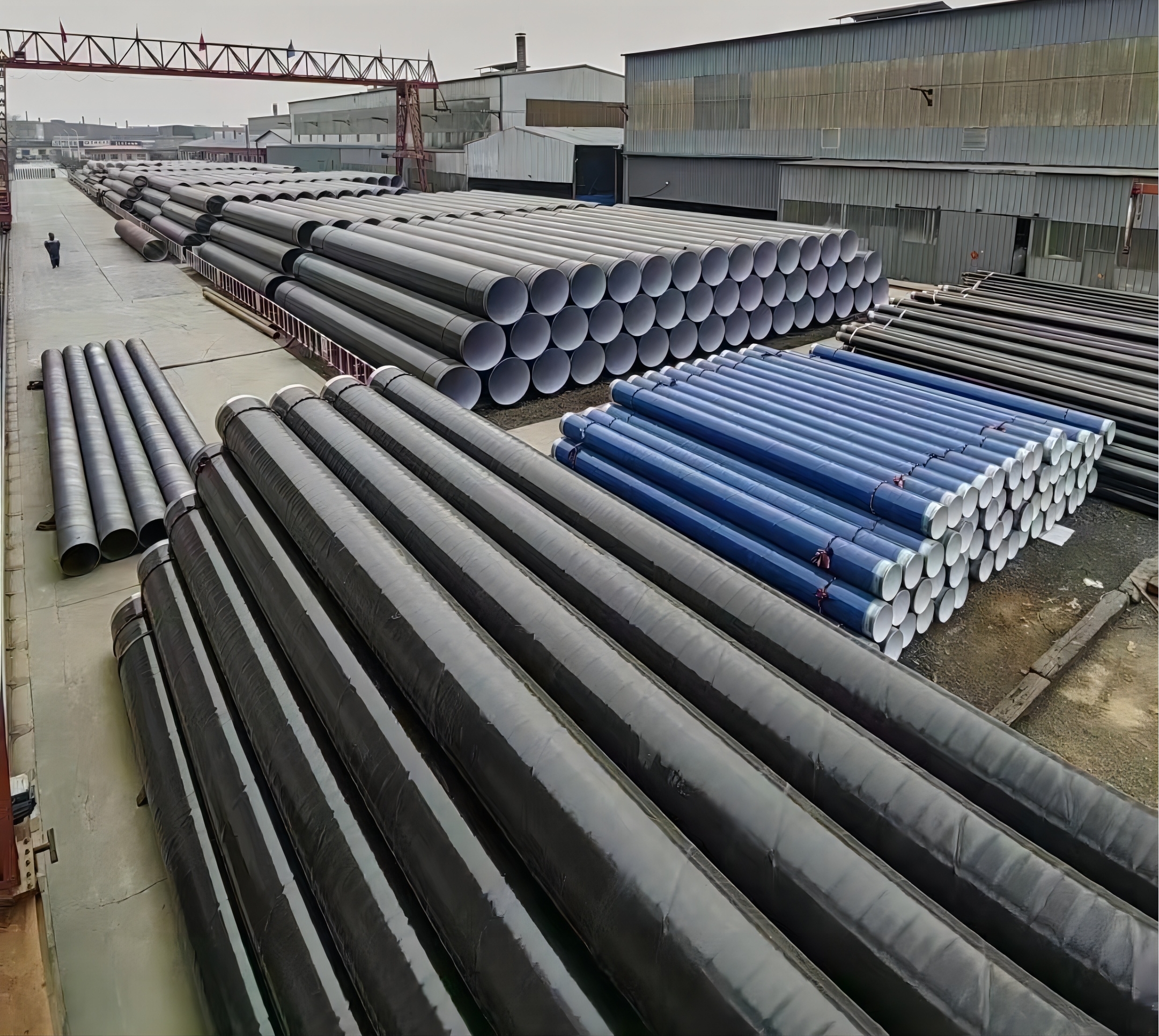
-
Veelvoorkomende problemen met coatingmaterialen
Veelvoorkomende problemen met coatings zijn onder meer het ongelijkmatig aanbrengen van de verf, het druppelen van corrosiewerende middelen en het ontstaan van luchtbellen.
(1) Ongelijkmatige coating: Een ongelijkmatige verdeling van corrosiewerende middelen op het oppervlak van de pijp resulteert in gebieden met een te dikke coating, wat leidt tot verspilling, terwijl dunne of niet-gecoate gebieden het corrosiewerend vermogen van de pijp verminderen.
(2) Druppelen van corrosiewerende middelen: dit fenomeen, waarbij corrosiewerende middelen als druppels op het oppervlak van de pijp stollen, heeft invloed op de esthetiek zonder rechtstreekse gevolgen voor de corrosiebestendigheid.
(3) Vorming van bellen: Lucht die tijdens het aanbrengen in het anti-corrosiemiddel wordt opgesloten, veroorzaakt bellen op het oppervlak van de pijp, wat zowel het uiterlijk als de effectiviteit van de coating beïnvloedt.
-
Analyse van problemen met de coatingkwaliteit
Elk probleem kent verschillende oorzaken en wordt veroorzaakt door verschillende factoren; en een bundel stalen buizen, waarvan de kwaliteit van het probleem naar voren komt, kan ook een combinatie van meerdere factoren zijn. De oorzaken van een ongelijkmatige coating kunnen grofweg worden onderverdeeld in twee soorten: de ongelijkmatige coating die ontstaat door het spuiten nadat de stalen buis de coatingbox is binnengegaan; de tweede is de ongelijkmatige coating die ontstaat door het niet spuiten.
De reden voor het eerste fenomeen is duidelijk te zien: de coatingapparatuur draait de stalen buis in de coatingkast 360° rond met in totaal 6 spuitpistolen (de mantelbuis heeft 12 spuitpistolen) om te spuiten. Als de spuitgrootte per spuitpistool verschilt, zal dit leiden tot een ongelijkmatige verdeling van het anticorrosiemiddel over de verschillende oppervlakken van de stalen buis.
De tweede reden is dat er naast de sproeifactor nog andere oorzaken zijn voor het fenomeen van een ongelijkmatige coating. Er zijn veel factoren, zoals roestvorming en ruwheid van stalen buizen, waardoor de coating moeilijk gelijkmatig te verdelen is. Het oppervlak van stalen buizen laat een waterdrukmeting achter wanneer de emulsie wordt aangebracht, dit keer voor de coating door contact met de emulsie. Hierdoor hecht het conserveermiddel zich moeilijk aan het oppervlak van de stalen buis. Hierdoor ontstaat er geen coating van de stalen buisdelen, wat resulteert in een ongelijkmatige coating van de gehele stalen buis.
(1) De reden voor hangende druppels anticorrosiemiddel. De doorsnede van de stalen buis is rond. Telkens wanneer het anticorrosiemiddel op het oppervlak van de stalen buis wordt gespoten, zal het anticorrosiemiddel in het bovenste deel en de rand door de zwaartekracht naar het onderste deel vloeien, wat het fenomeen van hangende druppels zal veroorzaken. Het goede nieuws is dat er ovenapparatuur is in de coatingproductielijn van de stalen buizenfabriek, die het anticorrosiemiddel dat op het oppervlak van de stalen buis wordt gespoten, tijdig kan verwarmen en stollen en de vloeibaarheid van het anticorrosiemiddel kan verminderen. Als de viscositeit van het anticorrosiemiddel echter niet hoog is; niet tijdig verwarmen na het spuiten; of de verwarmingstemperatuur niet hoog is; of de spuitmond niet in goede staat verkeert, enz., zal dit leiden tot hangende druppels anticorrosiemiddel.
(2) Oorzaken van anticorrosieve schuimvorming. Door de luchtvochtigheid in de werkomgeving is de verfdispersie te hoog. Een temperatuurdaling tijdens het dispersieproces kan leiden tot blaasvorming van het conserveermiddel. Een luchtvochtigheidsgraad van de omgeving en lagere temperaturen kunnen ertoe leiden dat conserveermiddelen in kleine druppeltjes uit de omgeving worden gespoten. Dit leidt tot een temperatuurdaling. Het water in de lucht met een hogere luchtvochtigheid condenseert na de temperatuurdaling tot fijne waterdruppeltjes vermengd met het conserveermiddel en dringt uiteindelijk in de coating, wat leidt tot blaasvorming.
Plaatsingstijd: 15-12-2023